Pros and Cons
Summary of advantages and disadvantages that should be known when using laser welding
Laser welding is not only superior in productivity to conventional welding methods, but also has a significant improvement in welding quality.In recent development of laser welding technology, the trend of gradually replacing traditional welding methods such as arc welding and resistance welding has become irreversible.In the next 21st century, laser welding technology will play a vital role in the field of material joining.
Welding principle
Laser welding uses a high-energy-density laser to illuminate the material at the junction of the heat source, thus, the separated material absorbs the laser energy and then rapidly melts or vaporizes and forms a molten pool,further solidified together in the subsequent cooling process to form a physics. Connection method.
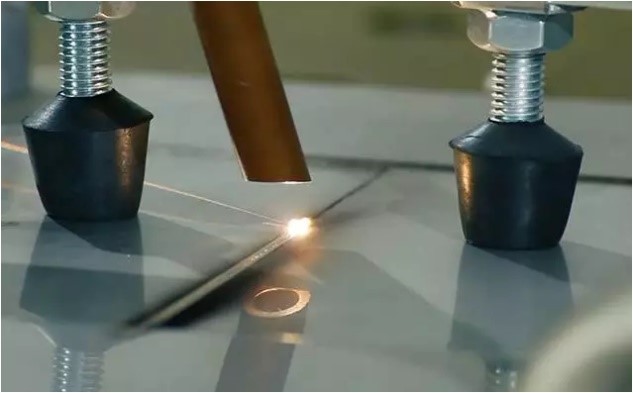
Laser welding Compared with other welding techniques, the main features of laser welding are:
- Fast speed, large depth and small deformation.
- It can be welded at room temperature or under special conditions, and the welding equipment is simple. For example, the laser passes through an electromagnetic field, and the beam does not shift; the laser can be soldered in vacuum, air, and a certain gas environment, and can be welded through glass or a material that is transparent to the beam.
- It can weld refractory materials such as titanium, quartz, etc., and can weld the foreign materials with good effect.
- After laser focusing, the power density is high. When welding high-power devices, the aspect ratio can reach 5:1 and the maximum can reach 10:1.
- Micro soldering is possible. The laser beam is focused to obtain a small spot, and can be accurately positioned, and can be applied to the mass welding of small and small workpieces that are automatically produced in large quantities.
- It can weld inaccessible parts and perform non-contact long-distance welding with great flexibility.
- The laser beam is easy to split the beam according to time and space, and can perform multi-beam simultaneous processing and multi-station processing, which provides conditions for more precise welding.
Whether it is arc welding, gas welding, electric resistance welding or brazing, there are some shortcomings . Laser welding also has certain limitations:
- The position of the weldment must be very precise and must be within the focus of the laser beam.
- The maximum weldable thickness is limited to workpieces with a penetration thickness of more than 19 mm. Laser welding is not suitable on the production line.
- Highly reflective and highly thermally conductive materials such as aluminum, copper and their alloys, the weldability will be changed by the laser.
- When performing medium-to-high-energy laser beam welding, a plasma controller is used to drive out the ionized gas around the bath to ensure re-emergence of the weld bead.
- The weld bead is rapidly solidified and may have pores and embrittlement concerns. The energy conversion efficiency is too low, usually less than 10%.
To adapt the increasingly complex welding environment and welding part, increase light energy conversion and reduce welding deformation and heat area, we have launched a cost-effective laser welding head with 3KW high power.
Performance characteristics:
- 60° adjustable sideshaft assist gas, spray angle effectively prevents metal oxidation of high temperature.
- Focusing arbitrary within 20mm range makes focus energy can be control and higher.
- The optional CCD can achieve welding positioning and welding seam real-time detection.
- Optimized optical configuration, collimation and focus dual water-cooling design, increasing life span.
- Multi-fiber interface can match all kind of lasers.
- Drawer-style lens holder design, changing protective glasses is faster and easier.