Solve the Focus Error
A Shortcut to Solve the Focus Error
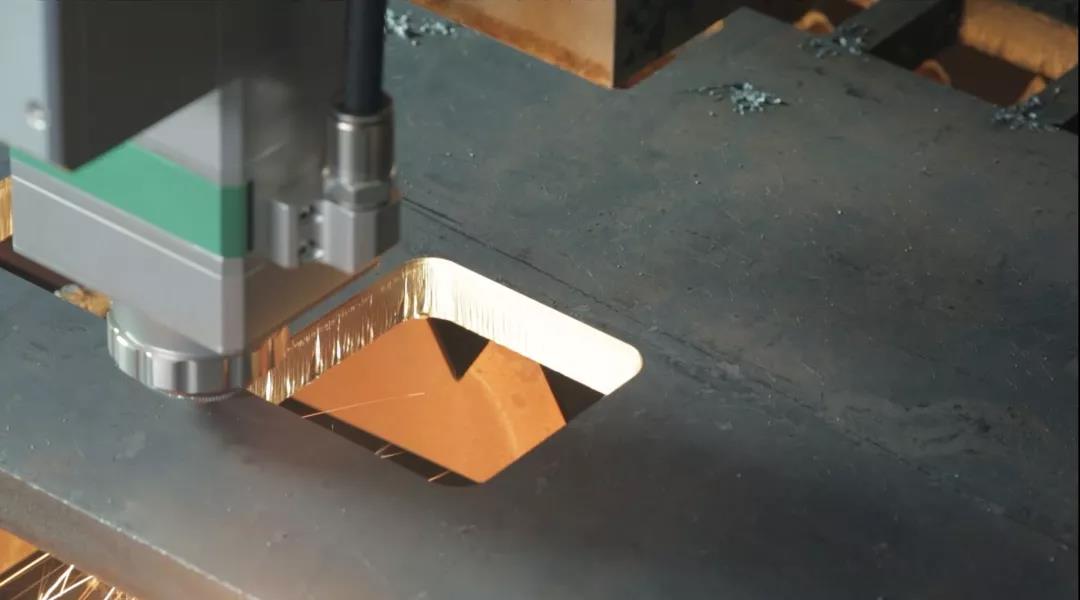
During laser cutting , there are many factors that cause a change in the relative position between the focus and the processed workpieces surface, including the surface of the workpiece is uneven , workpiece clamping method , geometric error of the machine tool and deformation of the machine tool under load, and the thermal deformation of the workpiece during machining. These will cause the laser focus position deviated from the ideal position (programming position).
Why have the Focus error
Some errors(Like geometric error of the machine)have regularity, they can be compensated by quantitative method, however, some errors are random and can only be eliminated by online monitoring and control.
1. Workpiece geometric error

Laser cutting objects are material sheet and covered components, because many factors will cause influences, the surface of the workpiece is uneven , and the thermal effect make the surface of thin plate deformed during laser cutting.For 1D laser processing , the covered component produces surface unevenness during depress forming.All of these will produce random changes in laser focus and ideal position of the object processed surface.
2. Workpiece clamping method produces error

Laser cutting workpieces are placed on the needle table.Due to machining errors, abrasion and laser burn between the workpiece for a long time, the needle bed will be uneven, and this unevenness will also produce a random position error between thin steel plates and laser focus.
2. Programming error
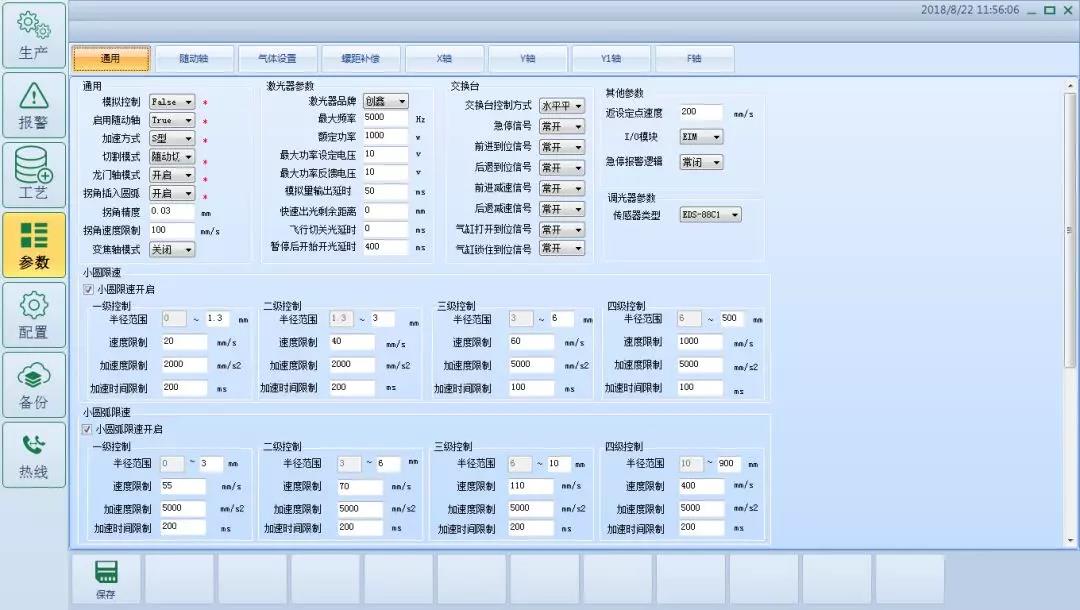
In the process of laser cutting, the processing trajectories on complex surfaces are fitted by straight lines, arcs, etc. There present certain errors between these fitting curves and actual curves to some extent. These cause relative position and ideal programming errors between the actual focus and the surface of the processing object, in addition, some teaching programming systems also have some deviations.
After years of development, the laser industry has a relatively perfect solution to the above-mentioned focus error. The laser can be manually adjusted on the laser head to adjust the laser focus. In addition, the current domestic laser head with automatic focusing function is also relatively mature, for use with a professional CNC system can help customers solve the error in laser cutting. Let's give a detailed introduction on how to adjust the focus position.
How to adjust the focus position
The laser cutting focus position online detection and control system is composed of controller, detection system and execution device and the like. The focus position detection control system is divided into two types: independent type and integrated type, also called manual focus adjustment and automatic focus adjustment.
1. Manual focus adjustment
The manual focus position detection and control system uses a separate coordinate axis to compensate focus position error. The mechanical structure is simple and the cost is low. It can be used with various CNC systems and laser cutting machines.
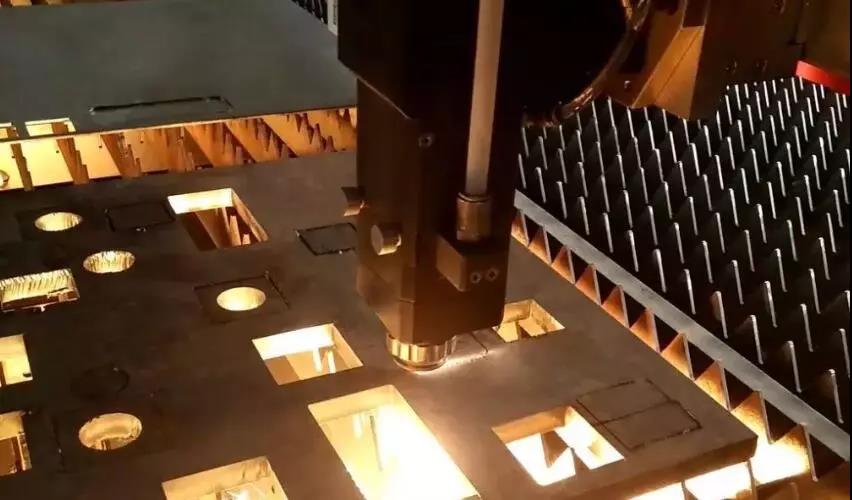
2. Auto focus adjustment
Autofocusing uses the combined motion of a feed axis or multiple feed axes through the laser cutting machine itself to compensate for focus position errors. This method has a relatively complicated structure and high cost, however, it is simple in operation and easy to adjust, and is required to be used in conjunction with a numerical control system.
The CNC software interface that supports autofocus controls the laser head to adjusts the focus by adjusting the parameters. This can reduce human intervention and make the focus position more accurate.
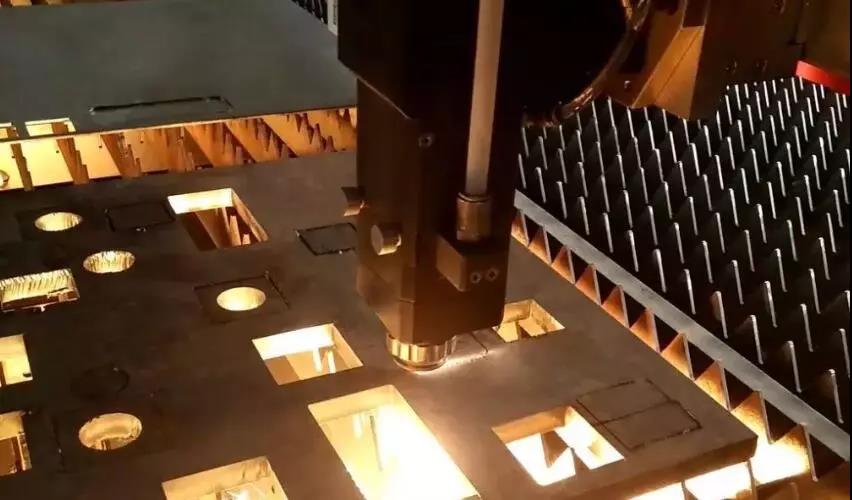
Corresponding system
The automatic focusing laser head requires a professional intelligent laser numerical control system to meet the needs of automatic focusing.
Professional automation control software can be free to add axis and control signal modules and provide customized main design functions.
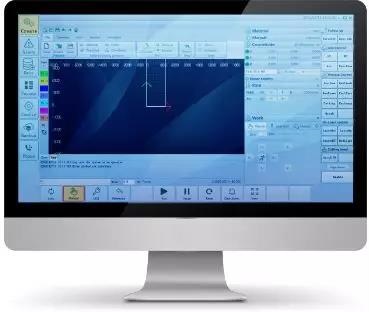